Construction Delays In Canada: Dow's Response To Market Instability
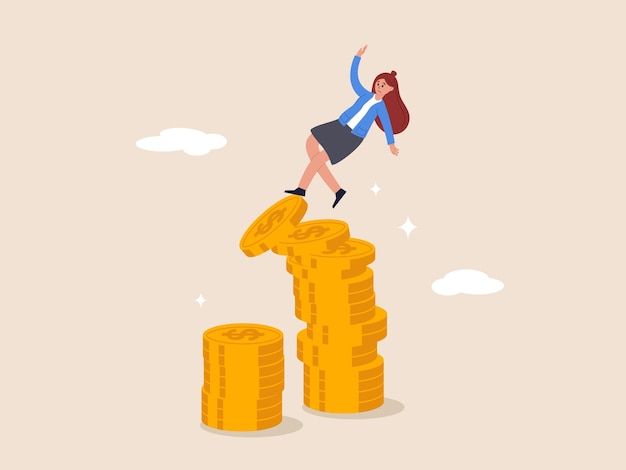
Table of Contents
Understanding the Root Causes of Construction Delays in Canada
Numerous factors contribute to the pervasive problem of construction delays across Canada. Let's delve into some key contributors:
Supply Chain Disruptions and Material Shortages
Supply chain issues have significantly impacted the Canadian construction industry, leading to widespread material shortages. This is largely due to:
- Increased lead times for key materials: The lead times for crucial materials like steel, lumber, and certain insulation products have dramatically increased, often delaying project starts and prolonging completion times. This is especially true for specialized materials used in complex projects.
- Global shipping challenges: Port congestion, container shortages, and global logistics bottlenecks have created significant delays in the delivery of construction materials to Canadian projects.
- Impact of tariffs: Trade disputes and tariffs on imported materials have increased costs and further exacerbated supply chain disruptions.
- Effects of labor shortages on material production: Labor shortages within the manufacturing sector have reduced the production capacity of many key construction materials, creating a ripple effect throughout the supply chain. This impacts the availability of
Canadian construction materials
across the board.
Labor Shortages and Skilled Trades Deficit
A significant contributor to construction delays in Canada is the persistent shortage of skilled labor. This stems from:
- Aging workforce: A significant portion of the Canadian construction workforce is nearing retirement, creating a gap in experienced tradespeople.
- Immigration challenges: While immigration can help address labor shortages, navigating immigration processes and ensuring skilled workers have the necessary credentials can be time-consuming.
- Lack of skilled labor: There is a demonstrable lack of skilled workers in various trades, leading to project delays and increased reliance on expensive subcontractors.
- Impact on project timelines: Labor shortages directly translate to longer project timelines and potential cost overruns.
Construction labor shortages in Canada
are consistently cited as a major factor in project delays. - Increased labor costs: The competition for skilled labor drives up wages, adding to project expenses.
- Training initiatives needed: Investing in robust training programs for new entrants to the construction workforce is crucial to address the skills gap. This is vital for the future of the
construction workforce in Canada
.
Regulatory Hurdles and Permitting Delays
Navigating the regulatory landscape in Canada can be complex and time-consuming, frequently contributing to construction delays. This involves:
- Complex permitting processes: Obtaining necessary permits and approvals often involves navigating multiple layers of bureaucracy and satisfying various regulations.
- Bureaucratic inefficiencies: Inefficient processes and lack of coordination between different government agencies can lead to significant delays in obtaining approvals.
- Environmental regulations: While essential, environmental regulations can sometimes lead to delays if not effectively integrated into project planning.
- Impact of differing provincial regulations: Variations in building codes and regulations across different Canadian provinces add complexity and can create unforeseen delays.
- Solutions for streamlining approvals: Implementing technology-driven solutions and streamlining approval processes can significantly reduce regulatory delays. Improving
construction permits in Canada
is key to faster project completion.
Unexpected Weather Events and Climate Change Impacts
The increasing frequency and severity of extreme weather events are adding another layer of complexity to construction projects across Canada. This includes:
- Increased frequency and severity of extreme weather: More frequent and intense storms, floods, and heat waves are disrupting construction schedules.
- Delays due to inclement conditions: Unforeseen weather events can halt construction activities for extended periods.
- Impact on project schedules and budgets: Weather-related delays inevitably lead to cost overruns and missed deadlines.
- Mitigation strategies: Proactive planning, utilizing advanced weather forecasting, and incorporating climate resilience into project design are crucial mitigation strategies. Effective
construction risk management in Canada
is paramount.
Dow's Strategic Response to Mitigate Construction Delays
Dow is taking a proactive and multi-faceted approach to mitigate the impact of construction delays in Canada. This includes:
Proactive Supply Chain Management
Dow is actively working to strengthen its supply chain resilience:
- Diversification of suppliers: Reducing reliance on single suppliers and diversifying sourcing minimizes the impact of individual supplier disruptions.
- Strategic stockpiling of key materials: Maintaining sufficient inventory levels of crucial materials helps ensure project continuity even during periods of supply chain stress.
- Improved forecasting and planning: Sophisticated forecasting models and advanced planning techniques allow for more accurate material ordering and scheduling.
- Partnerships with logistics providers: Collaborating with reliable logistics partners ensures timely delivery of materials, even under challenging circumstances.
- Transparent communication with clients: Open communication with clients helps manage expectations and mitigate potential disruptions. This ensures effective
construction material supply
despite challenges.
Investing in Technological Advancements
Dow is committed to leveraging technology to improve efficiency and reduce delays:
- Adoption of innovative construction technologies: Dow is actively involved in developing and promoting innovative construction technologies that improve efficiency and reduce waste. This involves the use of advanced materials and construction methods that improve project speed and reduce reliance on human labor.
- Improved efficiency and productivity: Implementing these technologies leads to significant improvements in construction efficiency and productivity.
- Reduced waste: Innovative solutions often minimize material waste, reducing costs and improving sustainability.
- Data-driven decision-making: Using data analytics enables better forecasting, planning, and resource allocation, minimizing the potential for delays. This is vital for the advancement of
construction technology in Canada
.
Strengthening Partnerships with Contractors and Developers
Collaboration is key to mitigating delays. Dow focuses on:
- Collaborative problem-solving: Working closely with contractors and developers to proactively identify and address potential challenges.
- Early engagement in project planning: Involvement in the early stages of project planning allows for the identification and mitigation of potential delays before they occur.
- Shared risk mitigation strategies: Developing shared strategies to manage and mitigate risks associated with potential delays.
- Open communication channels: Maintaining open and transparent communication channels ensures effective collaboration and problem-solving.
- Support for training and development: Dow supports initiatives to upskill the construction workforce and address labor shortages. This strengthens
construction partnerships in Canada
.
Conclusion: Mitigating Construction Delays in Canada with Dow
Construction delays in Canada present significant economic challenges, stemming from complex interactions of supply chain issues, labor shortages, regulatory hurdles, and climate change impacts. However, through proactive supply chain management, investment in technology, and strong partnerships with industry stakeholders, Dow is actively contributing to solutions. By collaborating on strategies that address the root causes of these delays, we can collectively work towards a more efficient and resilient Canadian construction industry. Reduce construction delays with Dow’s comprehensive solutions designed specifically for the Canadian market. Learn more about Dow's solutions for construction delays in Canada by visiting our website or contacting our representatives. Overcome construction delays in Canada – partner with Dow today.
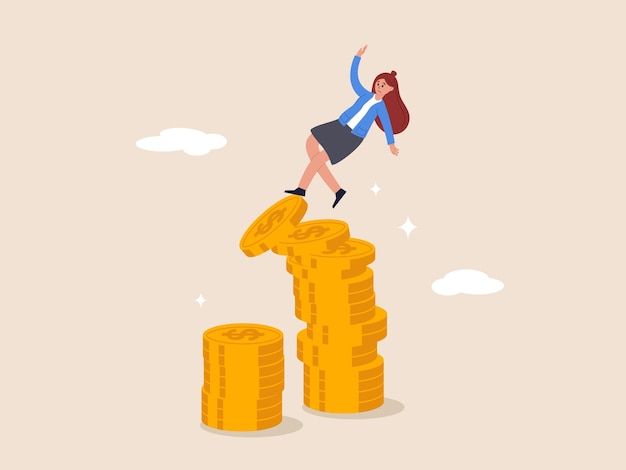
Featured Posts
-
Bucking Fastard Werner Herzogs New Film With A Real Life Sister Duo
Apr 27, 2025 -
Update World No 1 Sinner And The Doping Accusation
Apr 27, 2025 -
Napoleon Grills Canadian Manufacturing A Top Priority
Apr 27, 2025 -
Motherhood And Triumph Bencic In The Abu Dhabi Open Final
Apr 27, 2025 -
Understanding The Value Of Middle Management Benefits For Companies And Employees
Apr 27, 2025